Disclosure: As an Amazon Associate I earn from qualifying purchases. This page may contain affiliate links, which means I may receive a commission if you click a link and purchase something that I have recommended. There is no additional cost to you whatsoever.
A multidisciplinary workforce from Lawrence Berkeley National Laboratory (Berkeley Lab) has created a plastic that can be disassembled at a molecular stage utilizing an acidic resolution. Then, it may be reassembled with a brand new shade, texture, and form, many times. Unlike conventional plastic, which may solely be recycled two or thrice at most, this materials, known as poly(diketoenamine), or PDK, is infinitely recyclable.
Why is that this an necessary improvement? Plastics are making a waste administration disaster. Globally, we produce 380 million tons of plastic yearly, a lot of it for single use. Despite the presence of a recycling emblem on many plastic objects, less than 9% is recycled. Much of the plastic meant for recycling is shipped to Asia, creating a substantial transportation footprint. At the guts of the difficulty is that plastic — at the least till now — has not been infinitely recyclable and virgin plastic is commonly cheaper for producers than recycled.
“Most plastics have been by no means made to be recycled,” mentioned lead creator Peter Christensen, a postdoctoral researcher at Berkeley Lab’s Molecular Foundry. “But we’ve found a brand new option to assemble plastics that takes recycling into consideration from a molecular perspective.”
A Financial Incentive for Recycling
A new study from Berkeley Lab signifies that PDK might be commercially viable, making it extra prone to hit retailer cabinets someday quickly. The research discovered that virgin PDK is comparatively costly to make however that recycling prices are just like these of PET and HDPE. But PDK recycling prices are decrease than these of polyurethane, which curbside recycling packages don’t settle for. This value distinction would make recycling PDK much more interesting than landfilling it.
“We’re speaking about supplies which are mainly not recycled,” mentioned Scown. “So, when it comes to interesting to producers, PDKs aren’t competing with recycled plastic – they must compete with virgin resin. And we have been actually happy to see how low cost and the way environment friendly it is going to be to recycle the fabric.”
Because virgin plastic is so low cost, producers have little incentive to make use of recycled plastic. And the price of recycling has largely fallen on municipalities to shoulder as a result of there may be low demand and worth for recycled plastic. Manufacturers don’t have a lot motivation to make plastics extra recyclable as a result of they aren’t accountable for end-of-life product disposal. It’s a vicious cycle that encourages waste. Thus, most moldable — recyclable or not — results in landfills, at waste incineration vegetation, or as litter.
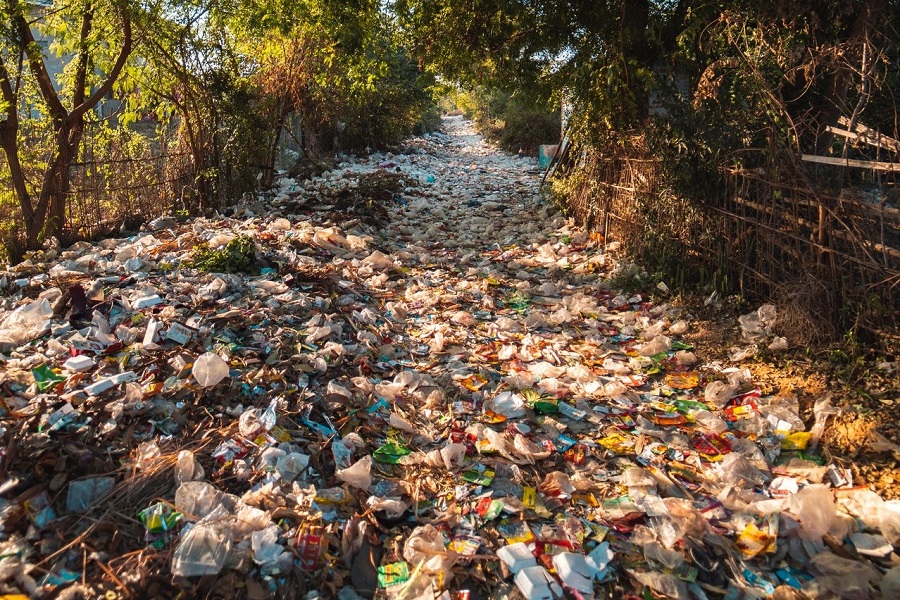
Introducing PDKs in Products
The Berkeley Lab workforce has created fashions to grasp the very best use of PDKs by producers. They conclude that the best functions are ones the place the producer takes again the product on the finish of life, like electronics and vehicle producers. Many of those corporations have recycling, trade-in, and take-back packages. This mannequin would permit producers to reap the advantages of next-generation polymers of their merchandise by long-term value financial savings and sustainable branding.
After introducing PDKs in sturdy items like electronics and automobiles, Berkeley Lab researchers hope to develop their use into single-use merchandise like packaging. Extended producer responsibility is an strategy that entails producers in the complete lifecycle of a product, together with end-of-life. This strategy helps embrace the round financial system and is a radical shift from the established order, particularly within the United States. Without prolonged producer accountability, most producers will choose to make use of the most affordable supplies, whatever the environmental and social impacts. This is as a result of the waste administration prices and environmental points within the U.S. usually don’t fall on producers.
“Some international locations have plans to cost hefty charges on plastic merchandise that depend on non-recycled materials,” says Corinne Scown of the Berkeley Lab workforce. “That shift will present a powerful monetary incentive to maneuver away from using virgin resins and will drive a number of demand for recycled plastics.”
Governmental insurance policies and shopper demand can assist gasoline the change wanted to drive greener enterprise practices. “These days, there’s a big push for adopting round financial system practices within the trade. Everyone is attempting to recycle no matter they’re placing out available in the market,” mentioned Nemi Vora, a postdoctoral fellow at Berkeley Lab. “We began speaking to trade about deploying 100% infinitely recycled plastics and have obtained a number of curiosity.”
Creating Recycling Infrastructure
The United States, the EU, New Zealand, Australia, Japan, and South Korea lack the infrastructure essential to recycle waste correctly. As a outcome, many recyclables have been being shipped to Asia for processing. In 2018, China instituted a ban on recycling imports.
After China’s bans, many developed international locations then diverted their waste to Southeast Asia, together with Thailand, Vietnam, Malaysia, and Indonesia, which lack the infrastructure, data, and insurance policies to deal with it correctly. Thus, the burden on the developed world’s trash remains to be ending up on seashores, waterways, and landfills abroad.
Ultimately, if PDKs show to be the neatest path ahead, plastics recycling must be reinvented for processing supplies that have been designed to be recycled. Additionally, home recycling infrastructure will should be created in order that the supplies are processed far nearer to the nation of origin. Then we are able to start to actually shut the loop on plastics recycling.